When it comes to securing mechanical components, you might find yourself choosing between a cotter key and a cotter pin. Both serve similar purposes but have distinct characteristics that can impact your project’s success. Understanding these differences can help you make informed decisions and ensure your assembly remains reliable.
Cotter keys and cotter pins each have unique designs and applications, making them suitable for various tasks. Whether you’re working on machinery, automotive projects, or DIY repairs, knowing when to use one over the other can save you time and frustration. Let’s dive into the key differences between cotter keys and cotter pins to help you select the right fastener for your needs.
Overview of Cotter Key and Cotter PIN
Cotter keys and cotter pins function as critical fasteners in various applications, providing stability and security in assemblies. Cotter keys consist of a straight or bent wire with a looped head, creating a locking mechanism when inserted through a hole. They require a second step to secure them by bending the prongs around an assembly part, preventing dislodgment.
Cotter pins feature a split design with a rounded head, allowing easier installation in single-step processes. When inserted, you bend the two prongs to secure the attachment, ensuring reliability and a strong hold.
Both components resist fatigue and wear, making them ideal for use in machinery and automotive projects. While cotter keys provide added security through their locking mechanism, cotter pins excel in applications where quick assembly and disassembly are essential. Understanding these attributes helps you select the right fastener for your specific needs.
Design and Structure
Understanding the design and structure of cotter keys and cotter pins aids in selecting the right fastener for your project. Each component has unique features that cater to different applications.
Cotter Key Design
Cotter keys consist of a straight or bent wire with a looped head at one end. The opposite end is tapered, allowing for easy insertion into holes of an assembly. After installation, you bend the prongs around the assembly part, forming a locking mechanism. The design ensures secure fastening, distributing loads evenly across the key’s structure. Cotter keys come in various sizes, accommodating different holes and load requirements, making them versatile for various applications.
Cotter PIN Design
Cotter pins feature a split design with a rounded head on one end and two prongs extending from the other. The rounded head allows for easy insertion, while the split prongs can be bent around an assembly to create a secure fit. This design enables simple installation in one step. Cotter pins are available in multiple sizes, providing options for various projects. Their design helps resist shear forces, ensuring reliability in applications where stability is critical.
Applications and Uses
Understanding the specific applications of cotter keys and cotter pins helps ensure the right fastener is chosen for your project. Each component has unique strengths suited to varying tasks.
Common Uses of Cotter Keys
- Agricultural Equipment: Cotter keys secure critical components like wheels and shafts, providing reliable fastening under heavy loads.
- Automotive Applications: Cotter keys hold together parts such as tie rods and suspension components, ensuring stability and safety.
- Construction Machinery: Cotter keys navigate the demands of heavy machinery, securing pins within hydraulic systems or supports to withstand high pressure.
- Marine Applications: Cotter keys fasten fittings within boats and marine equipment, resisting corrosion while withstanding the rigors of water exposure.
Common Uses of Cotter PINs
- Bicycle Assemblies: Cotter pins secure components like crank arms and derailleur hangers, facilitating easy assembly and maintenance.
- Home Appliances: Cotter pins maintain stability in appliances by securing various moving parts, ensuring consistent performance and safety.
- Industrial Equipment: Cotter pins fasten parts in assembly lines, allowing for quick replacements without sacrificing reliability.
- Sheet Metal Fastening: Cotter pins are effective in securing joint assemblies where a strong yet removable fastening solution is needed.
Recognizing these applications enhances your ability to choose the right fastener based on project requirements, conditions, and load expectations.
Advantages and Disadvantages
Understanding the pros and cons of cotter keys and cotter pins helps you select the right fastener for your project. Each has unique characteristics that can impact performance and suitability for specific applications.
Pros and Cons of Cotter Key
Pros:
- Strength: Cotter keys offer excellent strength in high-load applications, making them ideal for heavy machinery.
- Corrosion Resistance: Many cotter keys are made from materials that resist corrosion, ensuring durability in harsh environments.
- Secure Locking: The bent prongs provide a robust locking mechanism, preventing accidental disassembly.
Cons:
- Installation Complexity: Requires an additional step for securing, which adds time to the assembly process.
- Potential Damage: Improper bending can lead to damage of the cotter key or assembly component.
- Limited Reusability: Frequent removal and reinstallation may compromise their effectiveness, reducing lifespan.
Pros and Cons of Cotter PIN
Pros:
- Ease of Installation: Cotter pins allow for straightforward assembly in a single step, saving time during installation.
- Versatility: Available in various sizes, they suit multiple applications, from bicycles to industrial equipment.
- Low Maintenance: Simple design reduces the need for maintenance, making them user-friendly.
- Lower Load Capacity: Not always suitable for very high-load applications when compared to cotter keys.
- Risk of Displacement: If the prongs aren’t adequately bent, cotter pins can loosen over time, affecting their reliability.
- Less Secure: The split design may not provide the same level of security under heavy stress as cotter keys.
Conclusion
Choosing between a cotter key and a cotter pin ultimately boils down to your project’s specific needs. Each fastener has its strengths and weaknesses that can impact performance and longevity. Cotter keys excel in heavy-duty applications where secure locking is essential, while cotter pins offer simplicity and ease of use for lighter tasks.
By understanding the unique characteristics and applications of both components, you can make an informed decision that ensures the reliability and effectiveness of your assembly. Whether you’re working on machinery or tackling a DIY project, selecting the right fastener will enhance your results and help you avoid potential issues down the line.
Frequently Asked Questions
What is the primary difference between cotter keys and cotter pins?
Cotter keys consist of a straight or bent wire with a looped head, requiring a secondary step to secure. Cotter pins have a split design with a rounded head, allowing for single-step installation by bending their prongs. Both serve to secure assemblies but differ in installation methods.
Where are cotter keys typically used?
Cotter keys are commonly found in agricultural equipment, automotive applications, construction machinery, and marine setups. They are favored for their strength and corrosion resistance under heavy loads, making them ideal for harsh environments.
What applications are cotter pins suited for?
Cotter pins are frequently used in bicycle assemblies, home appliances, industrial equipment, and sheet metal fastening. Their easy installation and maintenance make them a popular choice in projects requiring reliable fastening without extensive effort.
What are the advantages of cotter keys?
Cotter keys offer robust strength, excellent corrosion resistance, and a secure locking mechanism for assemblies. They are ideal for heavy-duty applications but require more complex installation and may have limited reusability.
What are the benefits of using cotter pins?
Cotter pins are easy to install, versatile, and low maintenance, making them suitable for a variety of projects. However, they have a lower load capacity compared to cotter keys and may risk displacement if not secured properly.
How do I choose between cotter keys and cotter pins for my project?
Consider the load requirements, environmental conditions, and ease of installation. Use cotter keys for high-load applications where strength is crucial, and opt for cotter pins when simplicity and maintenance are priorities.
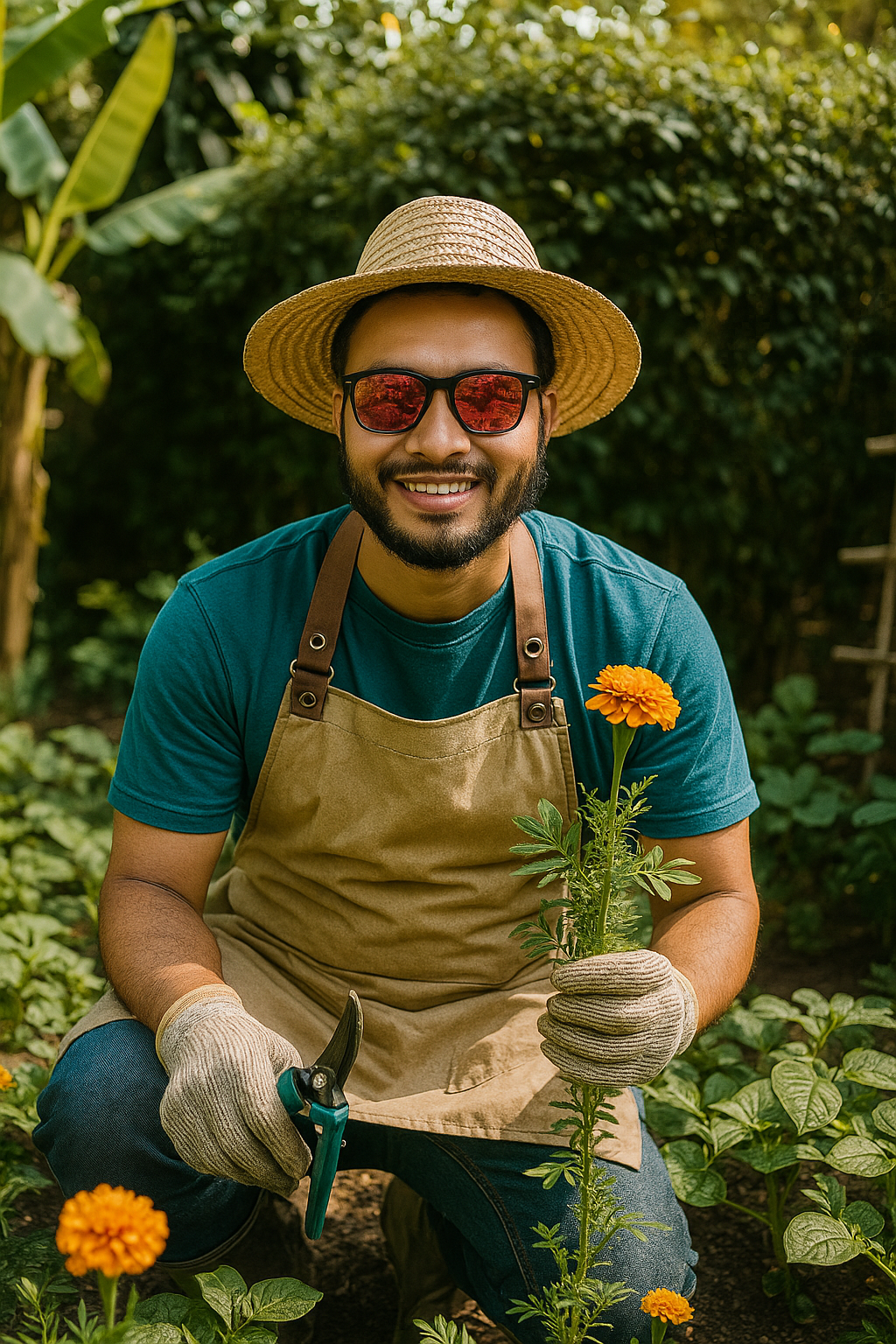
Hi, I’m Md Rofiqul, a gardening enthusiast who loves spending time in the garden and backyard. I enjoy caring for plants, growing flowers and vegetables, and creating a green space that feels peaceful and refreshing. Gardening is more than just a hobby, it’s a passion that connects me to nature and brings joy to my daily life. Living with plants inspires me to embrace simplicity, patience, and sustainability while making every day more colorful and rewarding.